Green Steel: What You Should Know
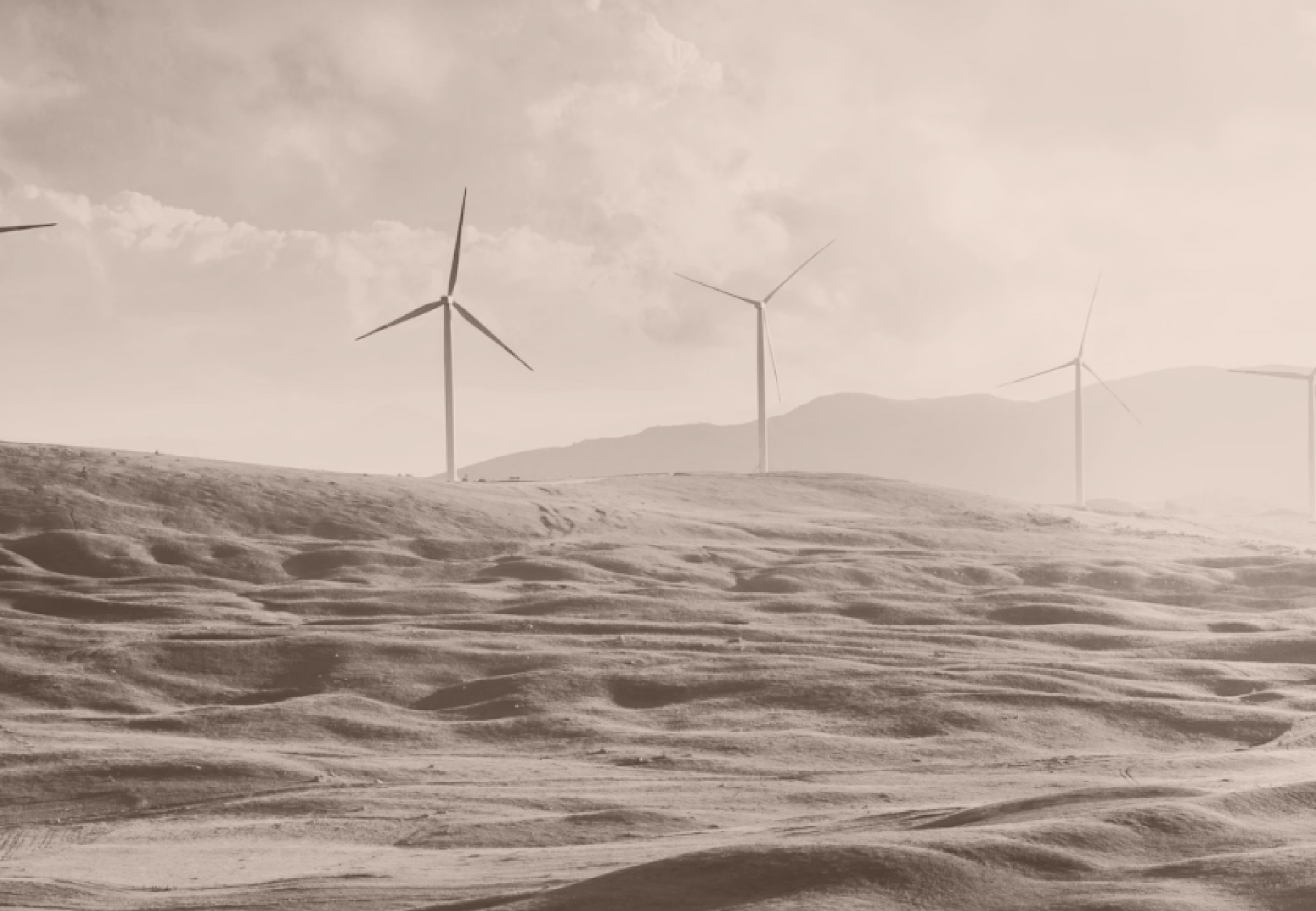
Steel is ubiquitous in the world around us. Without it, the things we take for granted in modern society — cars, consumer electronics, even office buildings — might not exist at all. But while steel is crucial for industry and infrastructure, its production has a substantial carbon footprint.
Steel production is responsible for around 8% of all greenhouse gas emissions globally — about as much as the entire country of India. On top of that, the industry is facing increasing pressure to decarbonise from customers, regulators, and investors.
The primary reason that steel production emits so much carbon is that the most common method of creating steel, a “blast furnace-basic oxygen furnace” (BF-BOF), relies heavily on coal, one of the world’s most carbon-intensive fossil fuels. In fact, coal makes up 89% of the energy input required for BF-BOF steel production.
Another method for steel manufacturing involves an “electric arc furnace” (EAF). Instead of iron ore, an EAF uses recycled steel scrap or direct reduced iron as its main input materials. This method requires coal for only 11% of its energy input. In the current steel market, however, the more carbon-intensive BF-BOF method represents 75% of all steel produced compared to only 25% for EAF.
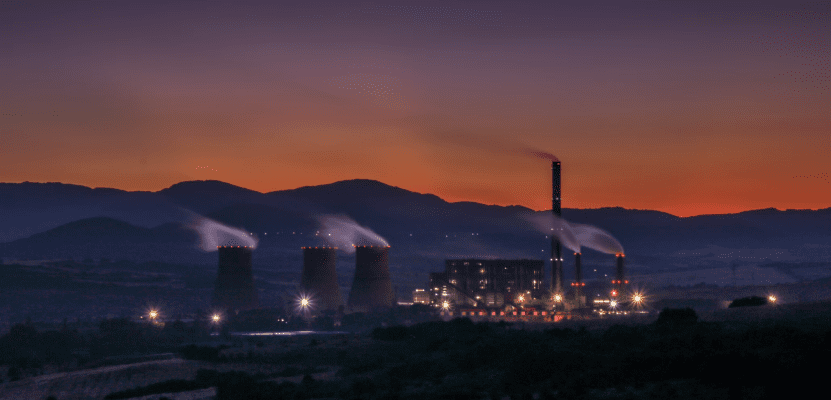
Considering global demand for steel is expected to increase significantly over the coming decades, steel producers around the world face difficult challenges in balancing both environmental and economic demands. To ease these pressures and satisfy the expectations of its various stakeholders, it is essential that the steel industry achieves breakthrough innovations in production technologies. The end goal: sustainable, coal-free, “green steel”.
To ease these pressures and satisfy the expectations of its various stakeholders, it is essential that the steel industry achieves breakthrough innovations in production technologies.
Steel & Renewable Energy Infrastructure
As countries around the world race to build renewable energy facilities to combat climate change, the steel industry’s large carbon footprint becomes particularly problematic.
To meet the climate targets established by the Paris Agreement, huge investments in renewable energy infrastructure will be required. But there’s a catch. Steel is a critical component of the wind turbines and solar panels needed in the coming decades, and the steel industry itself relies on the same fossil fuels renewable energy is trying to replace.
To compound this problem, the amount of steel that renewable energy infrastructure requires is enormous. An analysis by Bloomberg found that in order to build enough wind turbines to reach net-zero emissions by 2050, an amount of steel equivalent to 22,224 San Francisco Golden Gate Bridges would be needed. Building renewable energy infrastructure with coal-dependent steel would essentially cancel out any avoided carbon emissions from the renewable energy itself.
Using current technologies, an increase in steel production will directly result in an increase in carbon emissions. New technologies can change this reality by lowering the carbon intensity of steel and pushing the industry towards decarbonisation while expanding production to meet demand.
Can we reduce the carbon intensity of steel without innovation?
It is highly unlikely that the necessary carbon reductions can be achieved for the steel industry without finding a more sustainable way to produce steel. Without new technology, measures to reduce the carbon intensity of steel are limited to energy and material efficiency improvements — for example, increasing steel scrap collection and recycled material as opposed to producing steel from virgin iron ore.
The International Energy Agency recommends efficiency improvements only as a short to medium-term strategy for reducing carbon emissions for the industry. Furthermore, the Agency warns that “opportunities for further efficiency improvements will likely soon be exhausted”, and that new innovations in the next decade will be necessary to achieve significant emissions reductions.
There are reasons to be optimistic about breakthrough innovations for steel production, however. The demand for green steel — steel produced without the use of fossil fuels — has spurred action from a range of industry stakeholders, sometimes working together to achieve promising results.
Innovations in Green Steel
Swedish steel company HYBRIT made headlines in August of 2021 when it delivered the world’s first shipment of green steel to a customer, the car brand Volvo. Instead of coal, HYBRIT’s steel was produced using clean energy and hydrogen. “HYBRIT” is an acronym for “Hydrogen Breakthrough Ironmaking Technology“, and is a collaboration between: SSAB, a steel manufacturer; electric utility Vattenfall, and; LKAB, a mining company.
HYBRIT also received direct investment from the Swedish government to aid in the development of the company’s demonstration plant.
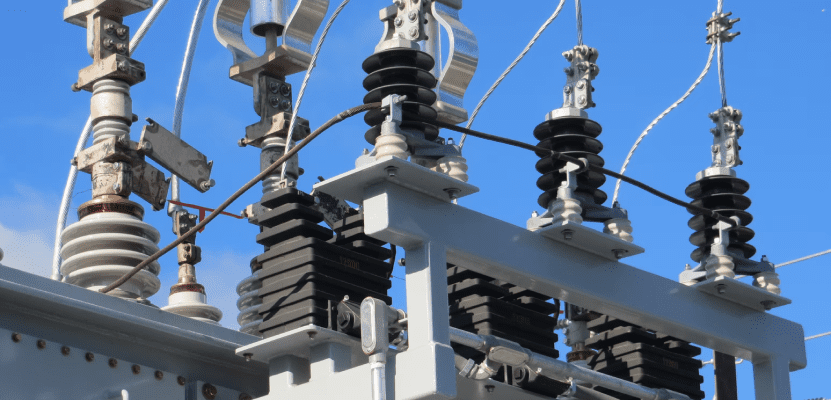
In the Netherlands, a pilot steel plant called HIsarna is testing a different approach to low-carbon steel. Using enhanced smelt-reduction technology, the steel produced from this plant would reduce carbon emissions and energy use by up to 20% compared to traditional methods. The technology could also be combined with carbon capture and storage, ensuring that any greenhouse gases emitted during manufacturing are not released into the atmosphere.
In the Netherlands, a pilot steel plant called HIsarna is testing a different approach to low-carbon steel.
“Electrowinning” is another innovative technology for producing steel that requires relatively little energy and emits very few greenhouse gases compared to traditional methods. Different variations of this process are being tested at facilities around the world. The Siderwin project in Europe, for example, is working to produce steel with zero direct emissions using this method. Initial tests for the pilot plant are expected to take place in early September of 2021.
The Role of Stakeholders
Though low- and no-carbon innovations have a long road ahead to achieving full adoption in the steel marketplace, the consensus is clear: it is crucial to scale these technologies as quickly as possible. New steel manufacturing sites have lifespans of more than 50 years, therefore the investment decisions in steel production technologies made today will play a critical role in limiting global warming by 1.5 degrees Celsius by 2050.
Reaching decarbonisation in the industry at the speed and scale necessary to curb climate change will require unprecedented effort from a wide range of stakeholders:
- Customers can prioritise suppliers that are investing in R&D to develop new steel technologies and/or offer steel products made from a high percentage of recycled material.
- Investors can pressure steel companies to disclose and improve their carbon performance.
- Governments can introduce carbon taxes to create market incentives for low and no-carbon steel.
With growing interest in new innovations and mounting pressure from all sides of the industry, a zero-carbon future for steel might just arrive sooner rather than later.